Designing for Manufacturability: Tips for Optimizing Your Plastic Parts
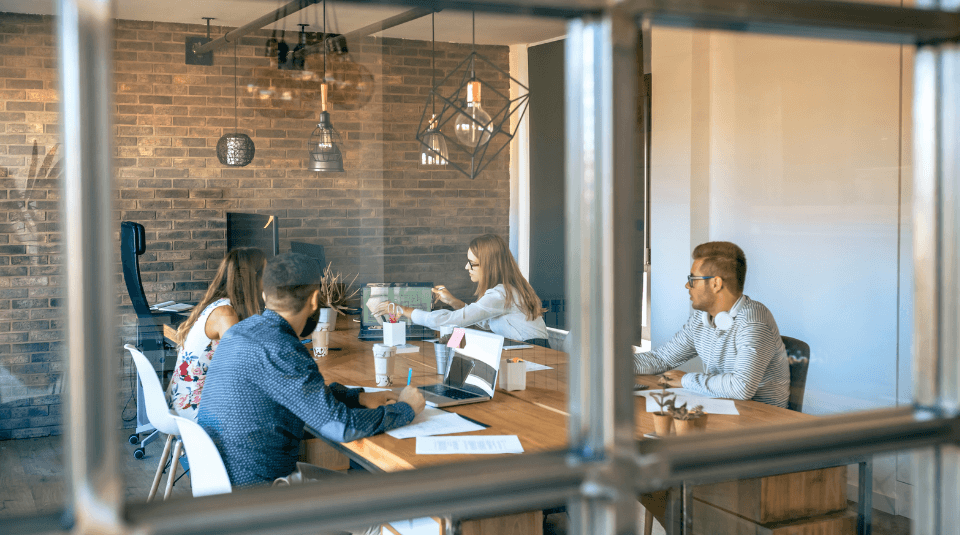
Designing plastic parts that are both functional and easy to manufacture can be a challenging task. However, by considering manufacturability early in the design process, businesses can save time and reduce cost while ensuring that their parts meet high standards of quality.
Design Considerations for Plastic Parts
There are several design considerations that can help optimize plastic part design for manufacturability. For plastic part design, it’s important to consider:
- Wall Thickness: Thicker walls can increase the strength of a part, but also increase cycle time and material usage. It’s important to balance wall thickness with other factors such as part function and cost.
- Draft Angles: Draft angles are tapered surfaces that allow parts to be easily ejected from the mold. Without draft angles, parts can become stuck in the mold and cause damage or defects.
- Undercuts: Undercuts are areas that prevent a part from being ejected from the mold in a straight line. When designing parts with undercuts, it’s important to incorporate features such as side actions or lifters that can be used to remove the part from the mold.
- Ribs and Bosses: Ribs and bosses are structural features that can increase the strength and stiffness of a part. However, it’s important to design them carefully to avoid sink marks or warping.
- Snap Fits and Living Hinges: Snap fits and living hinges can add functionality to a part, but they require careful design to ensure that they can withstand repeated use and not break or deform.
- Tolerances: Tolerances are the allowable variation in a part’s dimensions. Tighter tolerances can increase the accuracy and consistency of parts, but also increase the cost and complexity of manufacturing.
Plastic Mold Design
Mold design is in the success of plastic manufacturing. A well-designed mold can help ensure that parts are produced efficiently and to your desired specifications. When designing a mold for a plastic part, it’s important to consider factors such as mold material, gating design, and part ejection. The material used to make the mold should be selected based on factors such as durability, heat resistance, and cost. Gating design refers to the way that plastic is injected into the mold. The gating system should be designed to ensure that plastic flows smoothly and evenly into the mold cavity. Part ejection refers to how the part is removed from the mold.
The design of the ejector pins and parting lines can affect the final appearance and quality of the part. By designing a mold with manufacturability in mind, businesses can help ensure that their plastic parts are produced with efficiency and quality at the forefront.
Plastic Manufacturing Process
The plastic manufacturing process involves several steps, including material preparation, injection molding, cooling, and finishing. During material preparation, plastic pellets are heated and mixed before being injected into the mold. Injection molding involves the use of high pressure to force melted plastic into a mold cavity, where it cools and solidifies. After the part is ejected from the mold, it undergoes finishing processes such as trimming, painting, or assembly.
Quality Control in Plastic Manufacturing
Quality control is an important aspect of plastic manufacturing–it helps ensure that parts meet the required standards of quality and consistency. Quality control measures may include visual inspection, dimensional measurement, and material testing.
- Visual Inspection: Checking parts for defects such as cracks, sink marks, or warping.
- Dimensional Measurement: Ensuring that parts meet the required specifications for size and shape.
- Material Testing: Verifying that the plastic material meets the required specifications for properties such as strength, stiffness, and temperature resistance.
Optimize Your Parts with REO Plastics
Design for manufacturing or DFM requires careful consideration of part design considerations, the plastic manufacturing process, and quality control. By optimizing each of these factors, businesses can improve the efficiency, consistency, and quality of their plastic parts.
At REO Plastics, we are committed to providing high-quality plastic injection molding services that meet the unique needs of our customers–and we now have even more space to do so. Whether you need assistance with mold design, or quality control, our experienced team is here to help. Contact us today to learn more about how we can help you optimize your plastic parts for manufacturability.